The seal of sustainability Reduce, re-use, recycle
In an age where we’re all looking to use less plastic, we take our responsibility to the planet very seriously. We’re passionate about reducing the amount of plastic that is used in the first place.
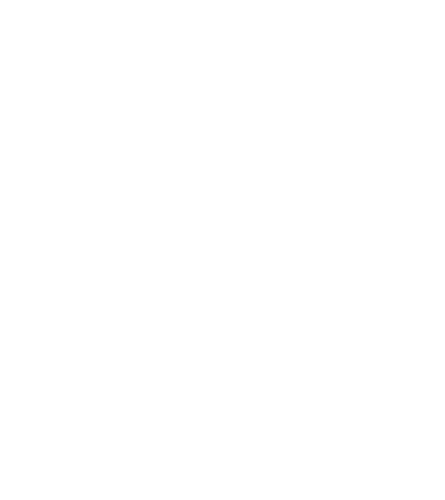
Start by using less resources
Our seals on average are 80% less than the mass of a rigid plastic clip seal. That’s 5 times less plastic before we even start looking at how to collect, recycle and re-use it. This means that if you’re sealing 15 million bags per year on one sealing machine, you’d use 2.3 metric tons of plastic less or 4.65 US tons less with our tape seals over a rigid plastic clip. Then add in the reduced costs for transport and storage and you can see that it’s a significant benefit.
Our passion means that we campaign to find new ways to collect, re-use and recycle as well as educating the consumer via BreadBags.org and working closely with food producers, supermarkets and environmental groups such as WRAP and the Plastics Pact
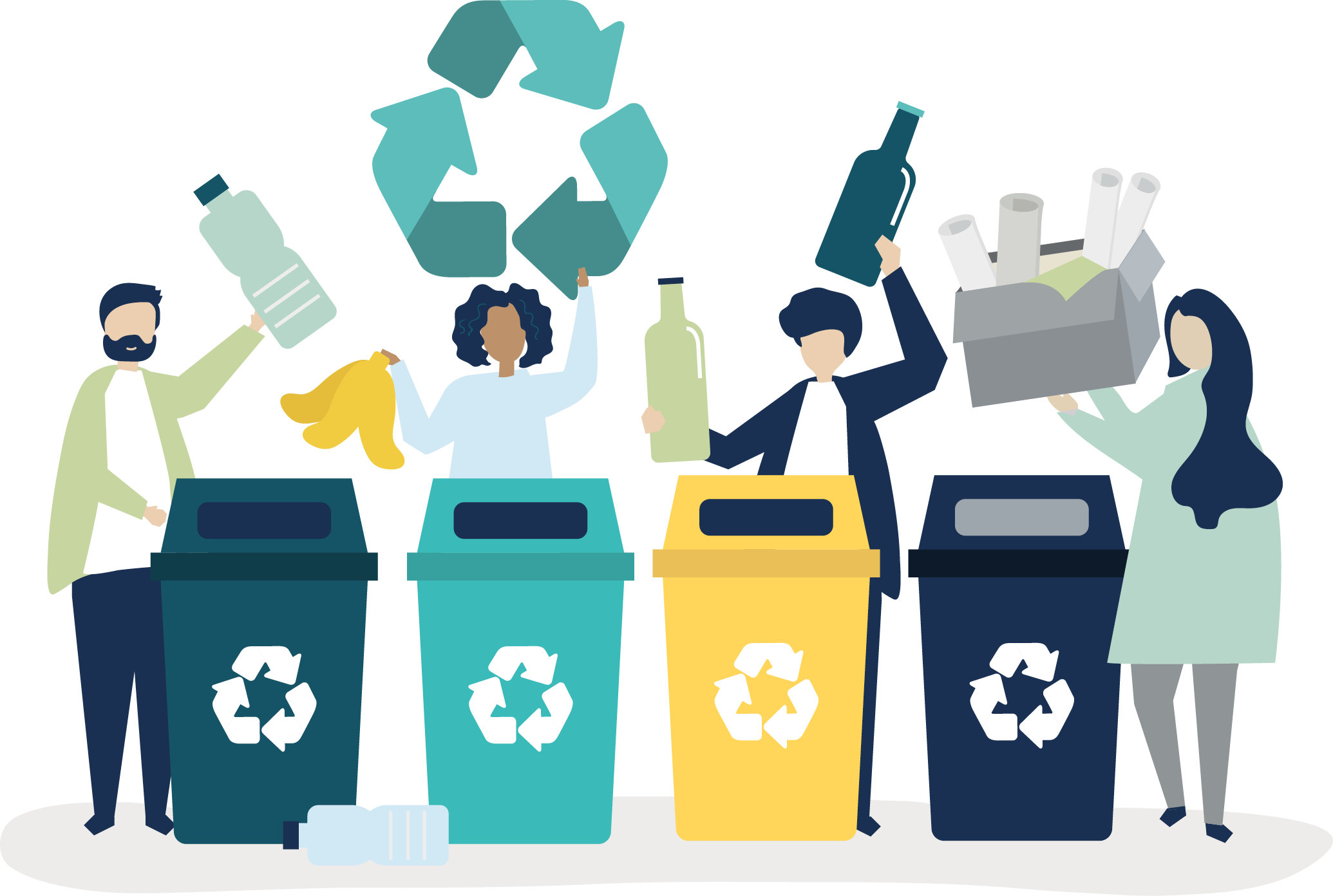
Working towards a
circular economy
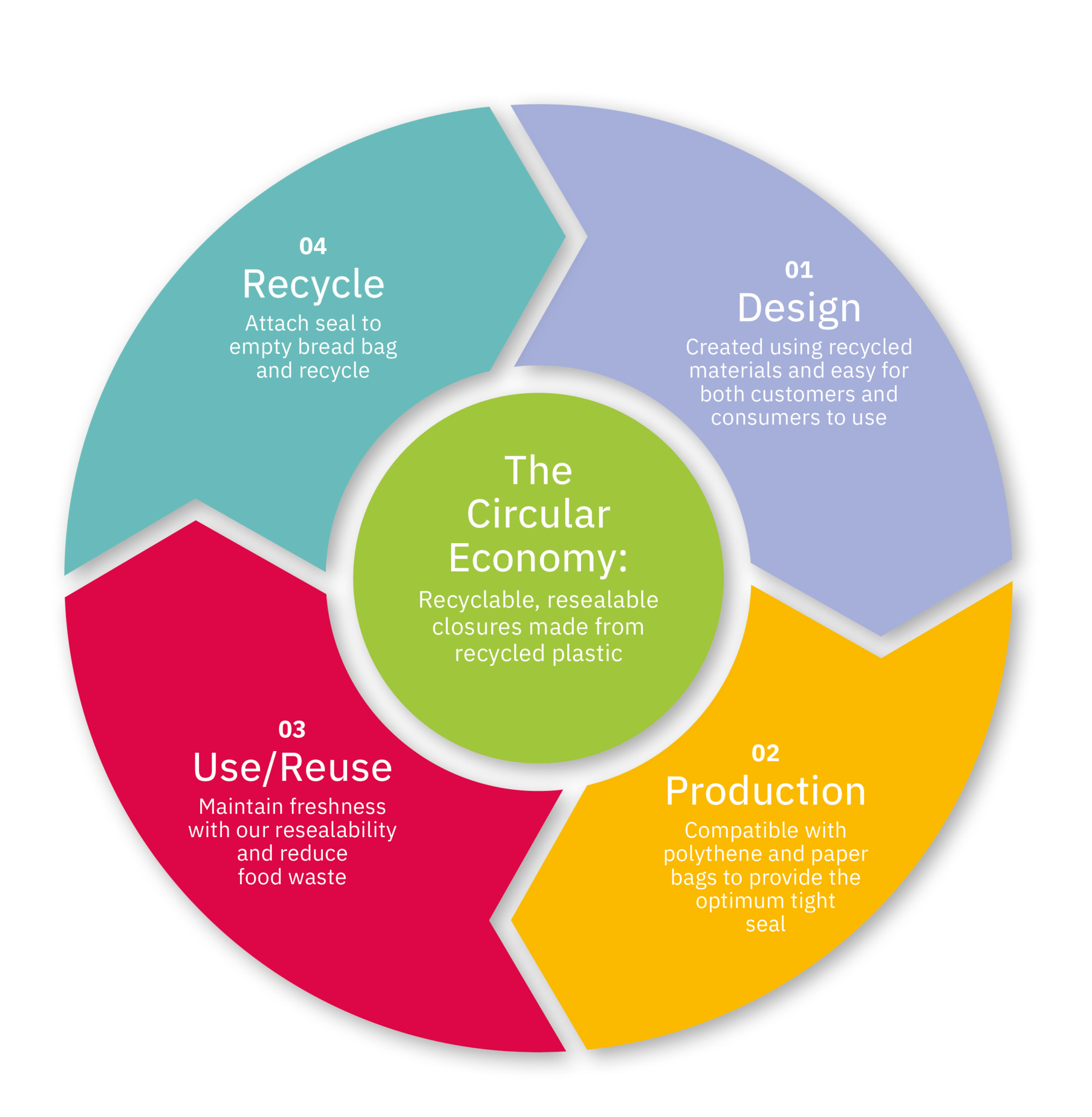
Proven to seal.
Re-seal. Recycle.
Our tape is made of polypropylene which is an easily-recycled plastic. We know this because polypropylene is already recycled and we’ve had our tapes tested by many plastic recycling companies. It also already contains 30% recycled plastic fulfilling government recycling requirements.
In the real world, our seals are attached to a polythene bread bag and typically represent less than 1% of total packaging. Although this means that PP, PE or LDPE plastics are effectively mixed, our tape is so small that it doesn’t compromise the ability to recycle the polythene.
Our tape is coated with a food safe adhesive that allows the seal to be opened and resealed 50+ times before the integrity of the seal and adhesive starts to decline. This resealability means that the food product can stay fresher for longer, reducing food waste too. Reassuringly this adhesive on the tape does not compromise it’s recyclability with either.
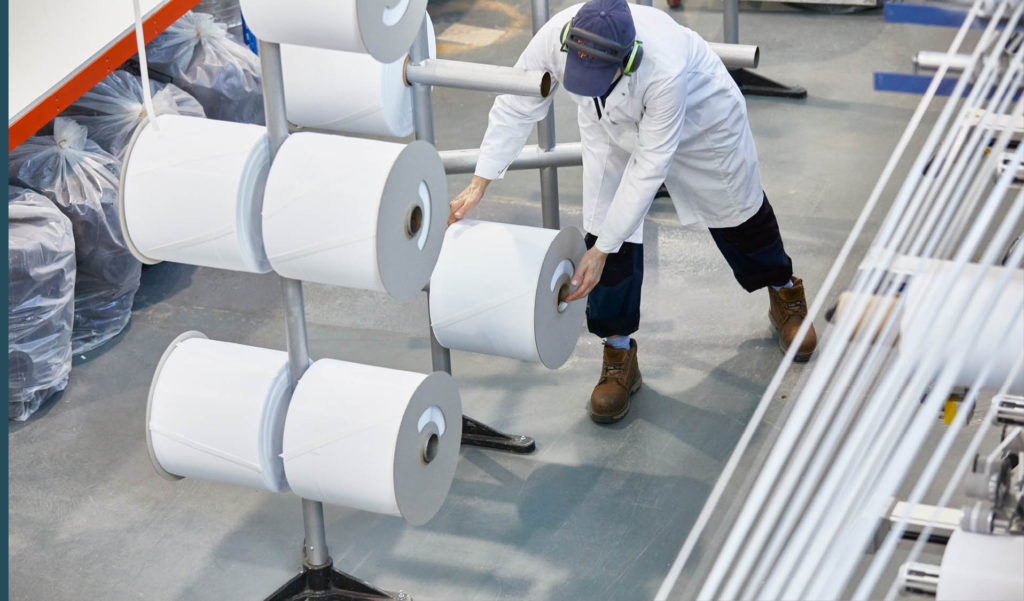
But why not remove plastic altogether?
While our tape seals and sealing machines are designed to work with paper bags, paper has inherent issues for sustainability, which are well documented. That’s why we still believe bagging bread in a polythene bag with our taped seal is the OPTIMAL method to maintain freshness. However you can be confident that our seals and machines work perfectly with paper bags too.
Responsible working as standard
The tape our seals are made from go through a number of technical processes which used to require input from a number of companies across Europe. 2021 saw us bring this whole process in house, further reducing the impact on the environment from transportation, reducing lead times and having greater control on output.
Being environmentally aware is an integral part of our DNA. Our field engineers all use PHEV or EV vehicles to minimise carbon emissions and we have installed charging points in our car park, for both company and private cars to use. To reduce our commercial impact on the environment further, we are also part of the Cycle to Work scheme and one third of our workforce are members.
But why not remove plastic altogether?
Responsible working as standard
Spreading the word
one seal at a time
We’re also working on initiatives to encourage retailers and manufacturers to collect bread bags with our seal attached, and inform and educate consumers about bread bag collection and recycling at BreadBags.org which we run in partnership with St John’s Packaging, worldwide manufacturers of bread bags.

Recycling the
non-recyclable
To help recycle the non-recyclable, we have also become a Terracycle
collection station and have invested in ISO 14001:2015 environmental
management accreditation. We also offer an ‘end of life’ service for
machines where we will remove and recycle machines to save you the
hassle and to ensure they are fully recycled wherever possible.
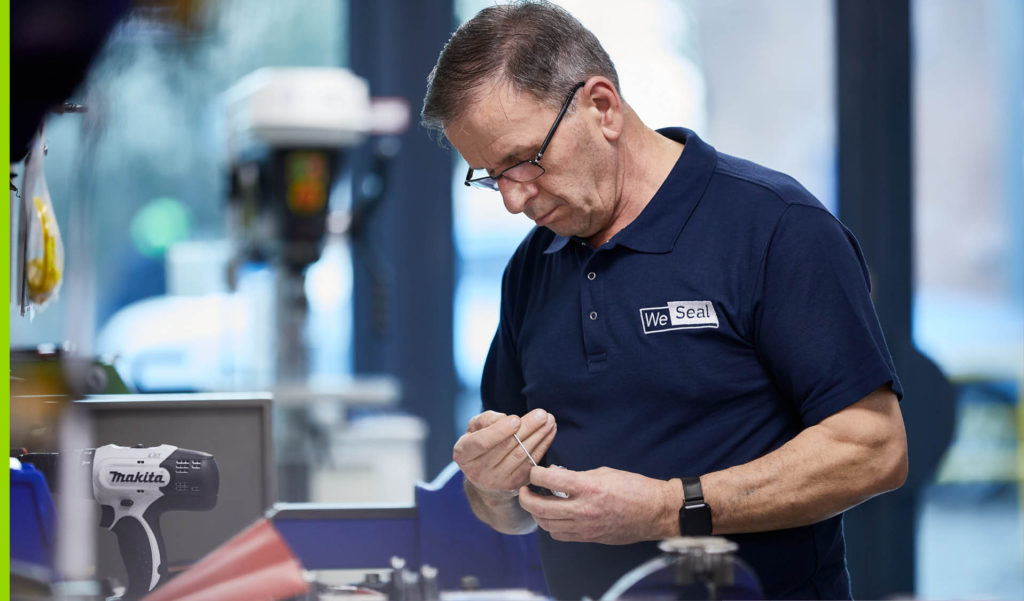